Bright (uncoated)
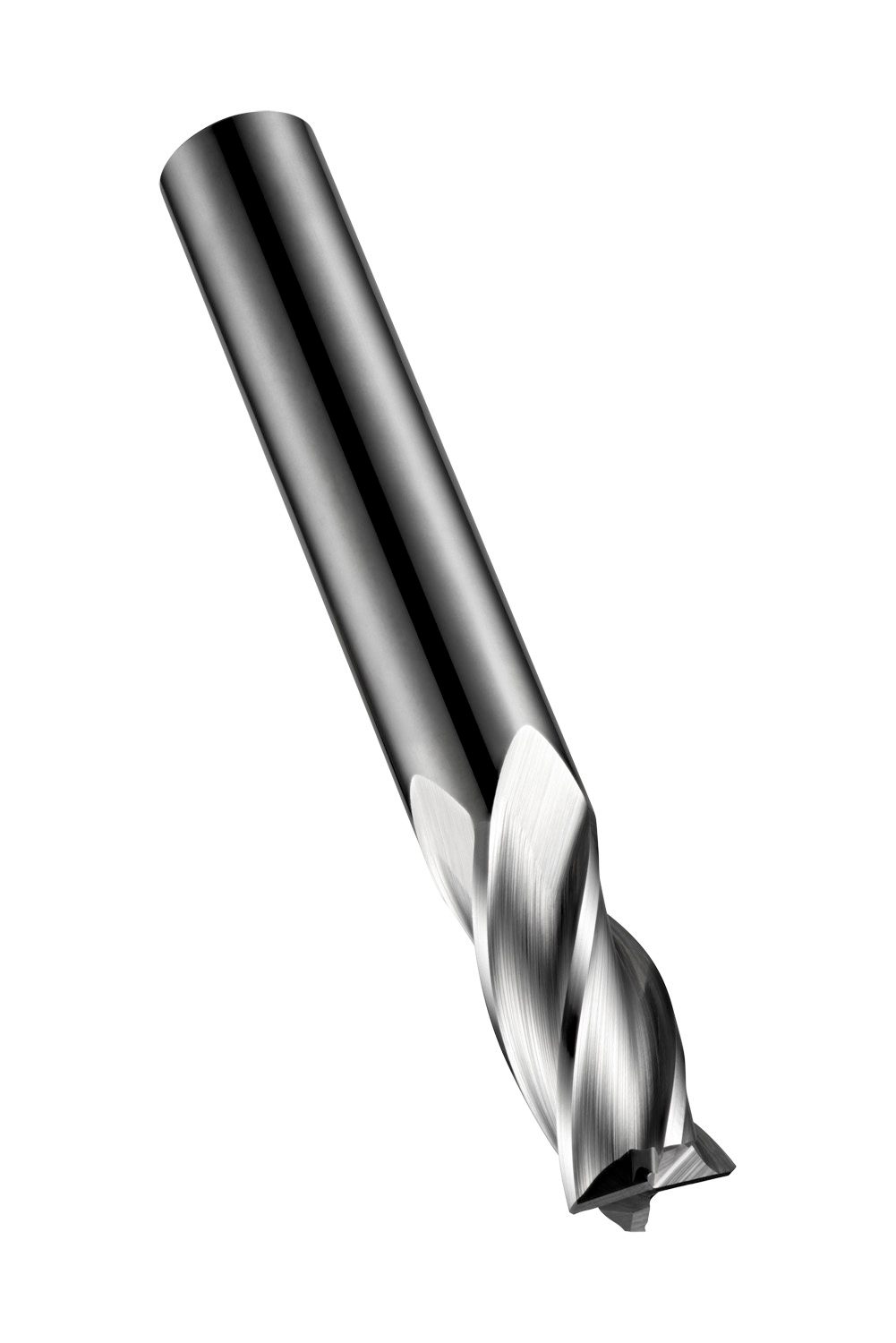
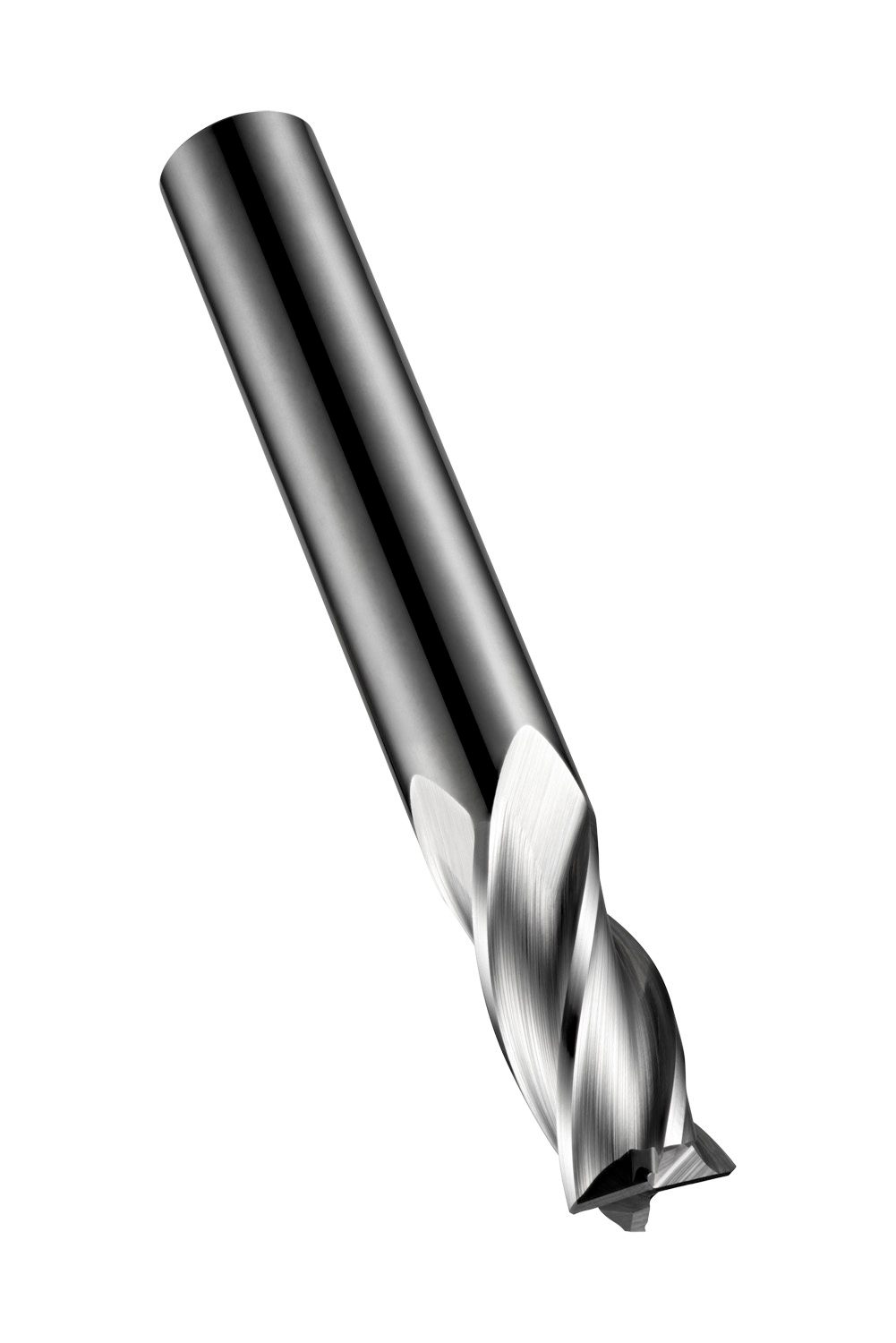
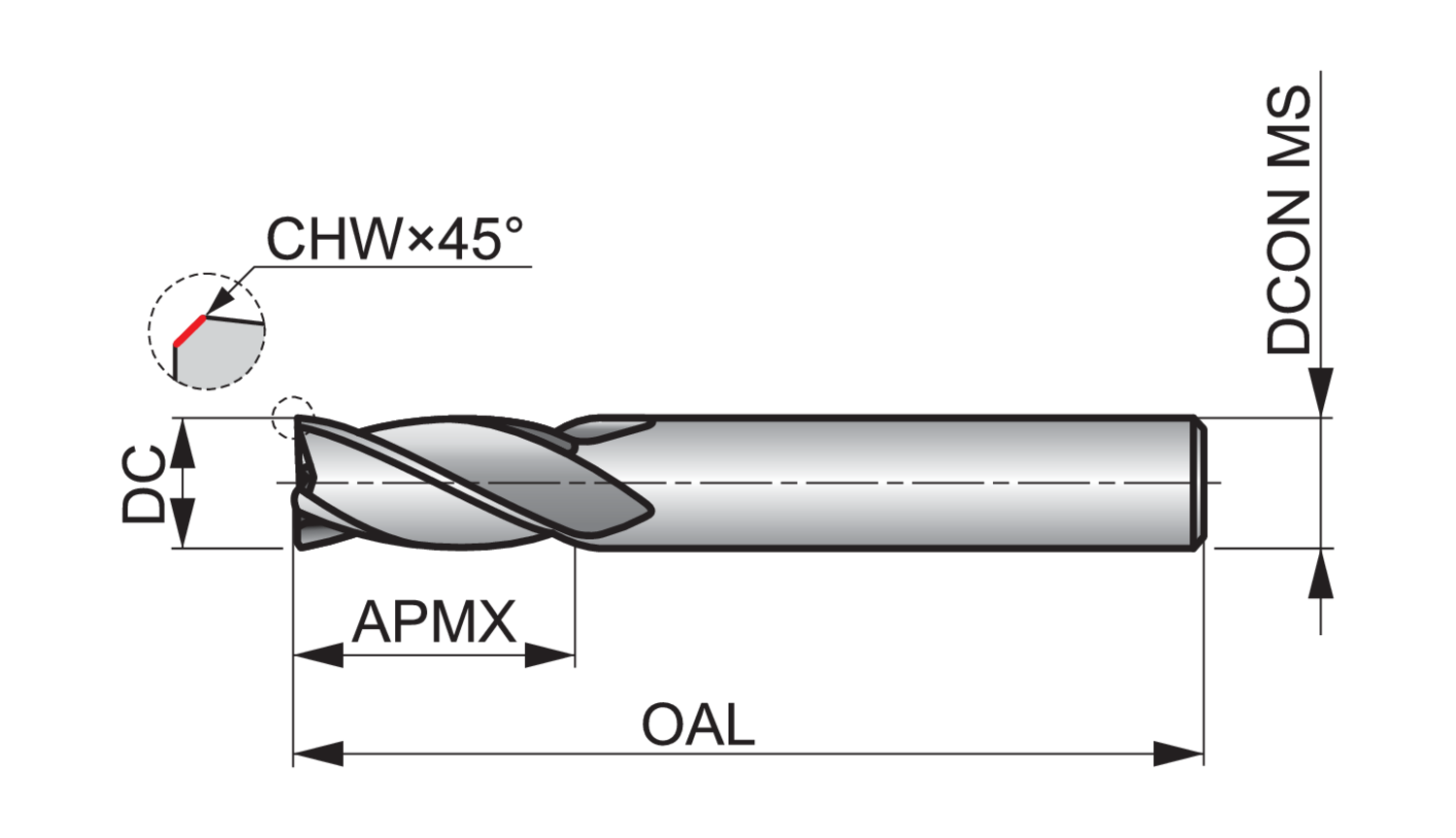
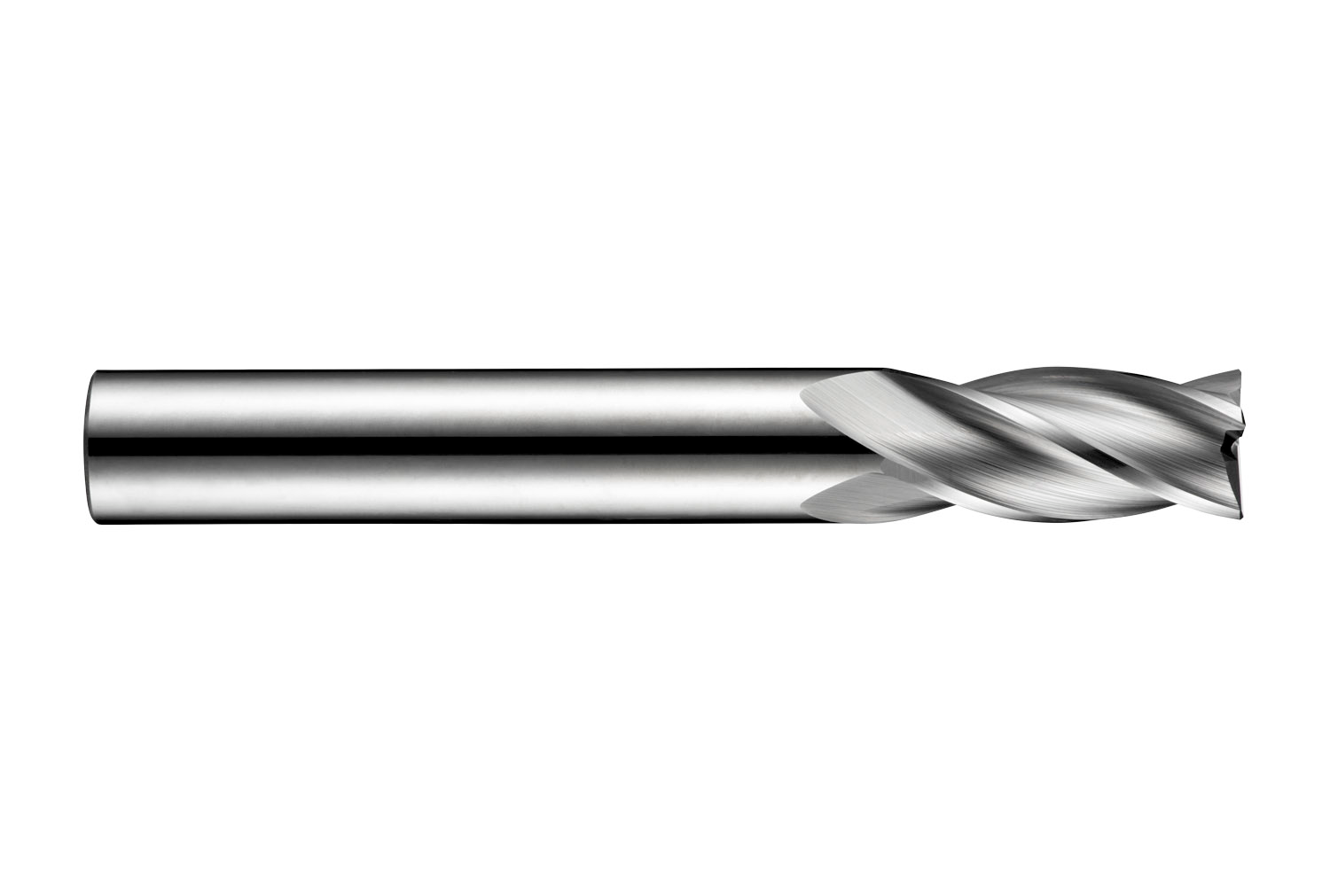
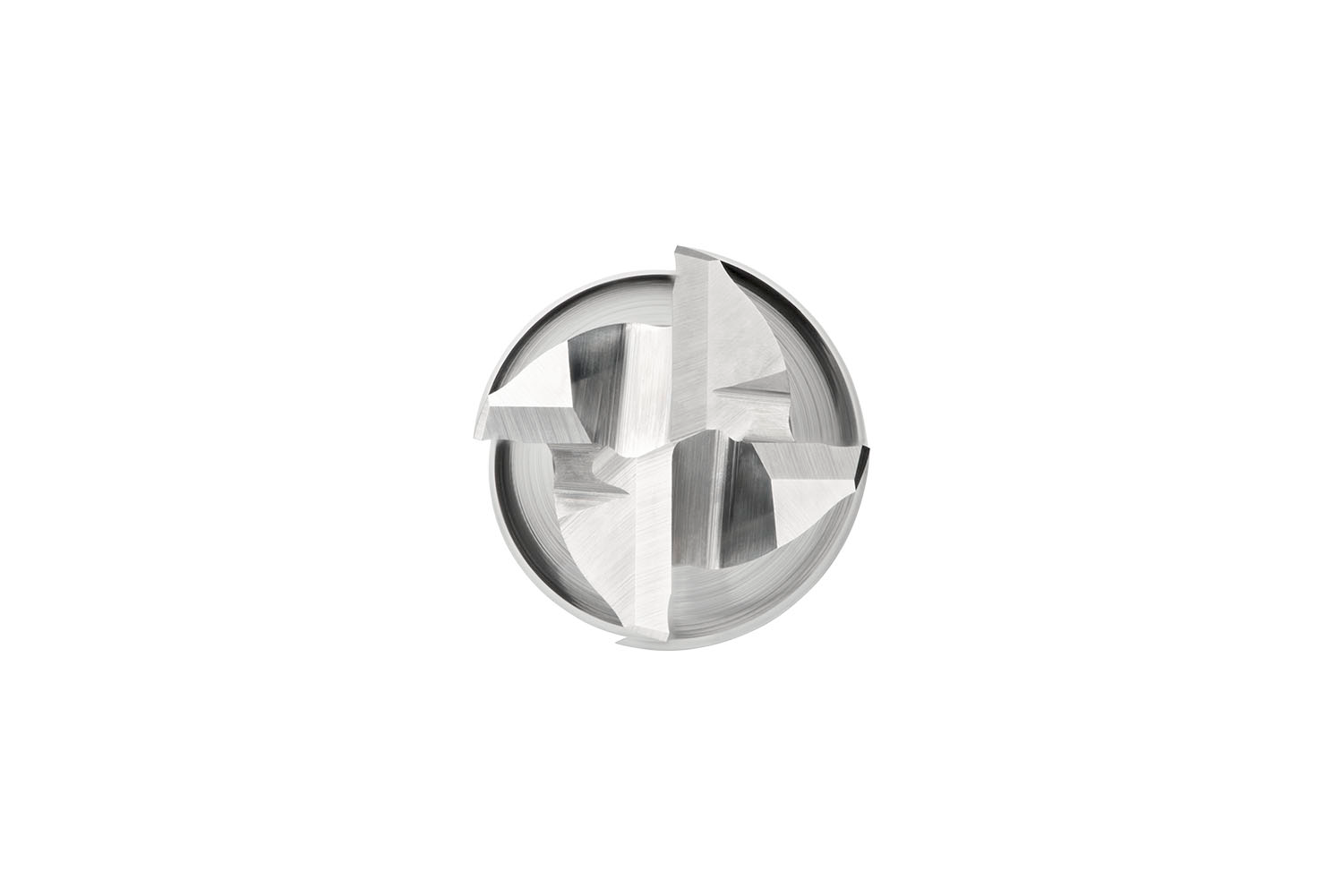
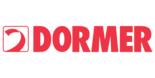
S90420.0
End Mill
Material ID: 5983167
Regular length end mill with 4 flutes, diameter 20mm with 38mm length of cut, 104mm overall length and 0.3mm 45° chamfered corner edges, according to DORMER standard with a 20mm plain shank, solid carbide with bright finish, 30° helix and 12° rake angle for shoulder milling in free machining, plain carbon and alloy steel, malleable, ductile and compacted graphite cast-iron and copper or copper alloys
Product Feature


Hard Material (Solid Carbide)

General Purpose Cutter Type for Low to High Resistance Materials

Cut Length, Medium

30° Helix Angle (Flute)

DIN 6535 HA Cylindrical Shank

h12 – Industry Standard Tool Tolerance Zone (based on diameter range)

Radial, Diagonal, Axial

Dormer Standards

Number of Flutes = 4 (teeth)
Product Operation

Shallow Shoulder Milling - Primary use

Deep Shoulder Milling - Possible use

Plunge Milling - Possible use

Shallow Slot Milling - Possible use

Ramping - Possible use

Progressive Plunging - Possible use
Product Detail
Description | Value |
---|---|
EAN number | 7320760133149 |
Product number (SAP) | 86020309 |
Ordering code ANSI | S90420.0 |
Gross weight - grams | 409.4 |
Cutting diameter - millimeter (DC) | 20 mm |
Corner chamfer width - millimeter (CHW) | 0.3 mm |
Connection diameter - millimeter (DCON MS) | 20 mm |
Depth of cut maximum - millimeter (APMX) | 38 mm |
Overall length - millimeter (OAL) | 104 mm |
Flute count (NOF) | 4 |
Radial rake angle (GAMF) | 12 |
ISO | S90420.0 |
Cutting Conditions
Suitability | vc | f | |
---|---|---|---|
P1.1 - Free machining sulfurized carbon steel with a hardness of < 240HB | Primary use | 106 m/min | 0.09 mm/rev |
P1.2 - Free machining sulfurized and phosphorized carbon steel with a hardness of < 180HB | Primary use | 119 m/min | 0.09 mm/rev |
P1.3 - Free machining sulfurized/phosphorized and leaded carbon steel with a hardness of < 180HB | Primary use | 123 m/min | 0.09 mm/rev |
Suitability | vc | f | |
---|---|---|---|
P2.1 - Plain low carbon steel containing < 0.25%C with a hardness of < 180HB | Primary use | 91 m/min | 0.09 mm/rev |
P2.2 - Plain medium carbon steel containing < 0.55%C with a hardness of < 240HB | Primary use | 80 m/min | 0.09 mm/rev |
P2.3 - Plain high carbon steel containing > 0.55%C, with a hardness of < 300HB | Possible use | 71 m/min | 0.073 mm/rev |
Suitability | vc | f | |
---|---|---|---|
P3.1 - Alloy steel with a hardness of < 180HB | Primary use | 66 m/min | 0.09 mm/rev |
P3.2 - Alloy steel with a hardness of 180 - 260HB | Primary use | 53 m/min | 0.073 mm/rev |
P3.3 - Alloy steel with a hardness of 260 - 360HB | Possible use | 45 m/min | 0.073 mm/rev |
Suitability | vc | f | |
---|---|---|---|
P4.1 - Tool steel with a hardness of < 26HRC | Primary use | 40 m/min | 0.073 mm/rev |
P4.2 - Tool steel with a hardness of 26 - 39RC | Possible use | 34 m/min | 0.073 mm/rev |
P4.3 - Tool steel with a hardness of 39 - 45HRC | Possible use | 18 m/min | 0.073 mm/rev |
Suitability | vc | f | |
---|---|---|---|
K1.1 - Gray iron, ferritic or ferritic-pearlitic with a hardness of < 180HB | Primary use | 80 m/min | 0.09 mm/rev |
K1.2 - Gray iron, ferritic-pearlitic or pearlitic with a hardness of 180 - 240HB | Possible use | 59 m/min | 0.09 mm/rev |
K1.3 - Gray iron, pearlitic with a hardness of 240 - 280HB | Possible use | 44 m/min | 0.09 mm/rev |
Suitability | vc | f | |
---|---|---|---|
K2.1 - Malleable iron, ferritic with a hardness of < 160HB | Primary use | 98 m/min | 0.09 mm/rev |
K2.2 - Malleable iron, ferritic or pearlitic with a hardness of 160 - 200HB | Primary use | 80 m/min | 0.09 mm/rev |
K2.3 - Malleable iron, pearlitic with a hardness of 200 - 240HB | Possible use | 64 m/min | 0.073 mm/rev |
Suitability | vc | f | |
---|---|---|---|
K3.1 - Ductile (nodular/spheriodal) iron, ferritic with a hardness of < 180HB | Primary use | 87 m/min | 0.09 mm/rev |
K3.2 - Ductile (nodular/spheriodal) iron, ferritic or pearlitic with a hardness of 180 - 220HB | Primary use | 67 m/min | 0.09 mm/rev |
K3.3 - Ductile (nodular/spheriodal) iron, pearlitic with a hardness of 220 - 260HB | Possible use | 54 m/min | 0.073 mm/rev |
Suitability | vc | f | |
---|---|---|---|
K4.1 - Austenitic cast iron with a hardness of < 180HB | Primary use | 81 m/min | 0.073 mm/rev |
K4.2 - Austenitic cast iron with a hardness of 180 - 240HB | Primary use | 61 m/min | 0.073 mm/rev |
K4.3 - Austempered ductile iron with a hardness of 240 - 280HB | Possible use | 45 m/min | 0.073 mm/rev |
K4.4 - Austempered ductile iron with a hardness of 280 - 320HB | Possible use | 38 m/min | 0.066 mm/rev |
K4.5 - Austempered ductile iron with a hardness of 320 - 360HB | Possible use | 32 m/min | 0.066 mm/rev |
Suitability | vc | f | |
---|---|---|---|
K5.1 - Vermicular, compacted graphite iron with a hardness of < 180HB | Primary use | 91 m/min | 0.073 mm/rev |
K5.2 - Vermicular, compacted graphite iron with a hardness of 180 - 220HB | Primary use | 69 m/min | 0.073 mm/rev |
K5.3 - Vermicular, compacted graphite iron with a hardness of 220 - 260HB | Possible use | 53 m/min | 0.073 mm/rev |
Suitability | vc | f | |
---|---|---|---|
N1.1 - Pure aluminium and wrought aluminium alloys with a hardness of < 60HB | Possible use | 355 m/min | 0.109 mm/rev |
N1.2 - Wrought aluminium alloys with a hardness of 60 - 100HB | Primary use | 267 m/min | 0.109 mm/rev |
N1.3 - Wrought aluminium alloys with a hardness of 100 - 150HB | Primary use | 179 m/min | 0.109 mm/rev |
Suitability | vc | f | |
---|---|---|---|
N2.1 - Cast aluminium alloys with a hardness of < 75HB | Primary use | 179 m/min | 0.09 mm/rev |
N2.2 - Cast aluminium alloys with a hardness of 75 - 90HB | Possible use | 160 m/min | 0.09 mm/rev |
N2.3 - Cast aluminium alloys with a hardness of 90 < 140HB | Possible use | 115 m/min | 0.09 mm/rev |
Suitability | vc | f | |
---|---|---|---|
N3.1 - Free-cutting copper-alloys materials with excellent machining properties | Primary use | 187 m/min | 0.09 mm/rev |
N3.2 - Short-chip copper-alloys with good to moderate machining properties | Primary use | 109 m/min | 0.09 mm/rev |
N3.3 - Electrolytic copper and long-chip copper-alloys with moderate to poor machining properties | Primary use | 56 m/min | 0.09 mm/rev |
Suitability | vc | f | |
---|---|---|---|
N4.1 - Thermoplastic polymers | Possible use | 187 m/min | 0.09 mm/rev |
N4.2 - Thermosetting polymers | Possible use | 72 m/min | 0.09 mm/rev |
Suitability | vc | f | |
---|---|---|---|
S1.1 - Titanium or titanium alloys, with a hardness of <200HB | Primary use | 38 m/min | 0.073 mm/rev |
S1.2 - Titanium alloys, with a hardness of 200 - 280HB | Possible use | 36 m/min | 0.073 mm/rev |
S1.3 - Titanium alloys, a hardness of 280 - 360HB | Possible use | 43 m/min | 0.066 mm/rev |
Suitability | vc | f | |
---|---|---|---|
S2.1 - High-temperature Fe-based alloys with a hardness of <200HB | Possible use | 40 m/min | 0.066 mm/rev |
S2.2 - High-temperature Fe-based alloys with a hardness of 200-280HB | Possible use | 35 m/min | 0.066 mm/rev |
Suitability | vc | f | |
---|---|---|---|
S3.1 - High-temperature Ni-based alloys with a hardness of <280HB | Possible use | 30 m/min | 0.066 mm/rev |
S3.2 - High-temperature Ni-based alloys with a hardness of 280 - 360HB | Possible use | 25 m/min | 0.066 mm/rev |
Suitability | vc | f | |
---|---|---|---|
S4.1 - High-temperature Co-based alloys with a hardness of <240HB | Possible use | 23 m/min | 0.066 mm/rev |
S4.2 - High-temperature Co-based alloys with a hardness of 240 - 320HB | Possible use | 20 m/min | 0.066 mm/rev |