CIE Automotive India transforms axle milling performance, lifting productivity and saving 38% on the total cost of cutting
Dormer Pramet delivers certainty in production efficiency
Key Outcomes
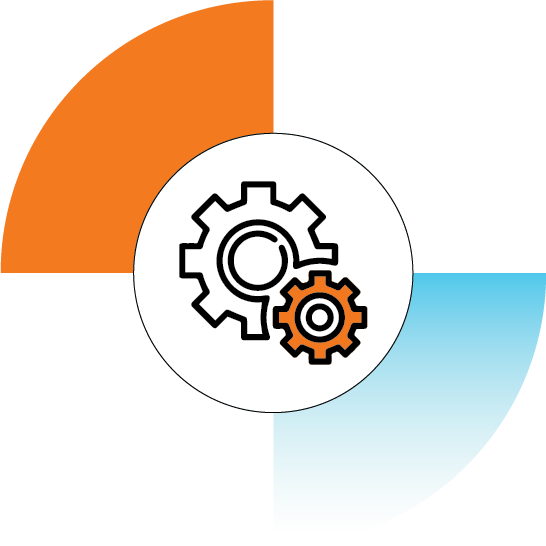
275%
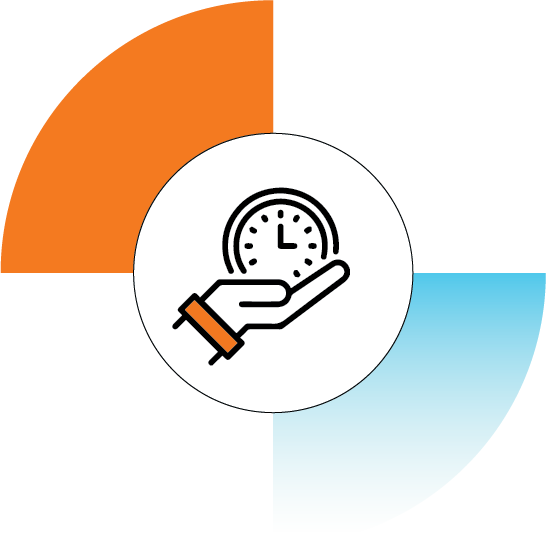
33%
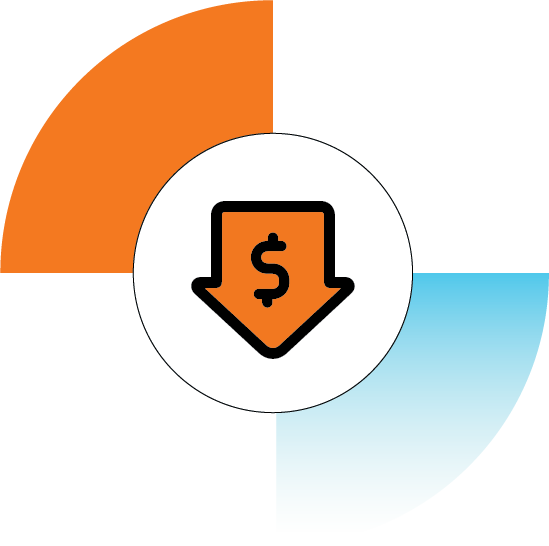
38%
Customer
Based in Pune, CIE Automotive India is a multi-technology supplier of auto components and sub-assemblies, making six out of 10 crankshafts and steering knuckles sold in the subcontinent. It also competes in the agricultural, railway, mining, and construction sectors. CIE Automotive India is a subsidiary of Spanish group CIE Automotive, which has a global footprint across 14 countries in four continents.
Challenge
CIE Automotive India was grappling with issues related to finish quality on tractor axle components which led to a high number of rejected pieces.
The key project objectives were to:
- Reduce cycle time by at least 25
- Improve finish quality
- Extend tool life
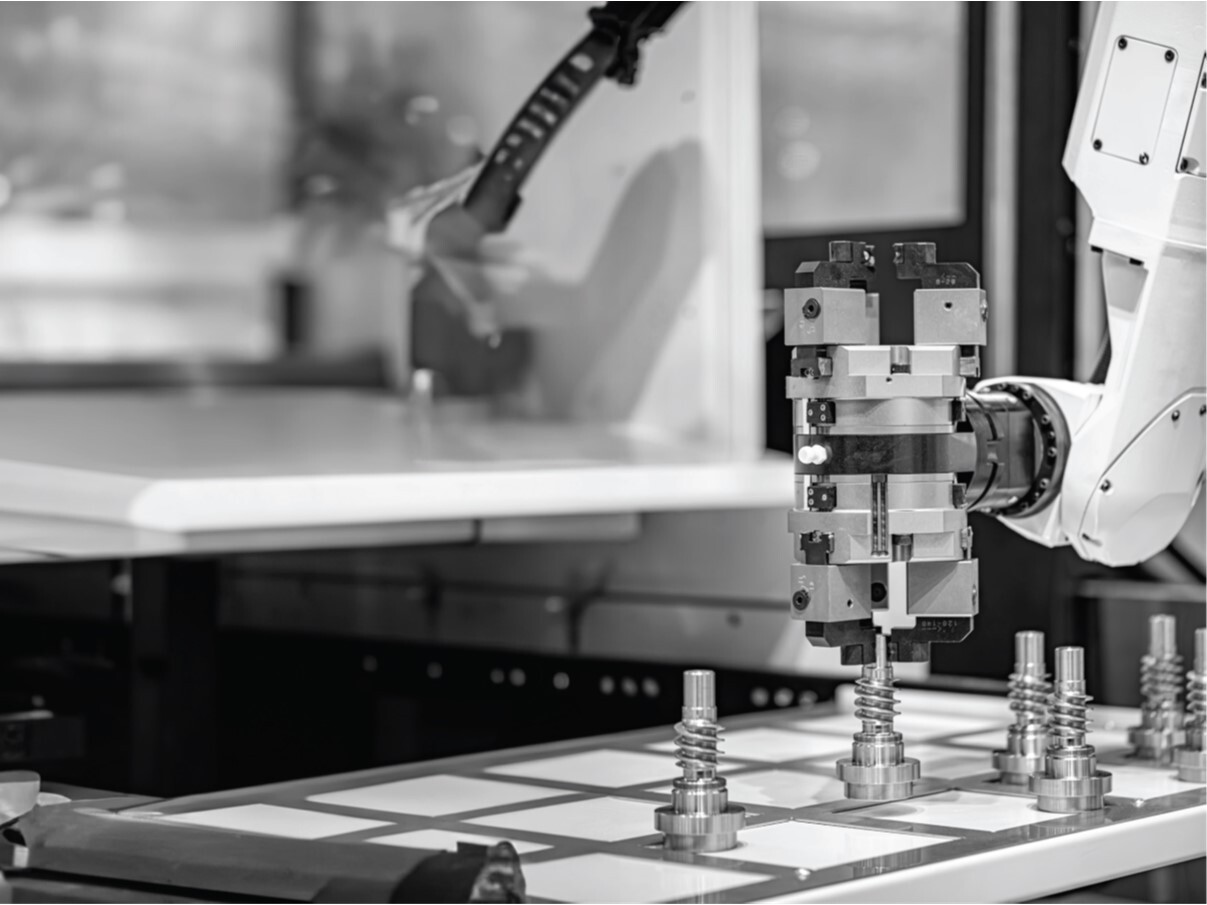
Solution
Dormer Pramet collaborated with CIE Automotive India to help them achieve increased quality and productivity by implementing improved tooling and optimised cutting techniques. In addition to providing highly productive and competitively priced solutions for machining automotive grade cast iron, Dormer Pramet worked with its local distribution partner to ensure superior product availability so the customer could obtain tools within 24 hours.
The solution included the 125A10R-S45ON06-C face mill and ONMX 060508SR-M:M8330 milling insert.
-
New-generation hardware Dormer Pramet's new-generation indexable face-milling tool proved superior to the competition in terms of cutting speed, finish quality, tool life, and flexibility.
-
Certainty in knowledge The on-site project team provided deep technical knowledge, collaborating with the business to design and apply a more efficient, consistent milling process.
-
Certainty in process Training was provided to teach setters and operators how the machine tool and workpiece should be set up and exactly how the process should run in terms of up-milling, down-milling, and stepover.
-
Certainty of support Dormer Pramet's distributor, Endeavour Technologies, provides local support and ensures CIE Automotive India can access the products it needs when it needs them. It also provides quick delivery of replacement parts.
-
Certainty in production efficiency Dormer Pramet's solutions have reduced tooling costs while also reducing cycling times and improving finishing quality.
Dormer Pramet solutions include:
Face Mill 125A10R-S45ON06-C
Milling Insert ONMX 060508SR-M:M8330
Benefits
Longer tool life means lower costs
Dormer Pramet inserts last nearly four times longer than previous tools used (30 cuts before replacement, up from 8). This has significantly reduced tooling costs.
Reduced scrappage rates
Improved finishing quality resulting from better tooling and a better, more consistent milling process has reduced scrappage rates. This, in turn, lowers operational costs and enables more accurate planning.
Top-notch customer service
Dormer Pramet’s local distributor, Endeavour Technologies, provides reliable support and delivery of replacement parts in 24-48 hours.
Faster cycle time
Dormer Pramet’s face-milling tool and a redesigned process have shortened cycle times by 33.5%. The volume of SG Iron (Group K, hardness 260 HB) cut per minute was measured at 27 cm3 versus 18 cm3 by the competitor insert.
New opportunities to increase productivity
Encouraged by these positive results, CIE Automotive India is now collaborating with Dormer Pramet to apply its tools and expertise to turning, hydra drilling, and other milling applications in order to extend productivity gains across the enterprise.
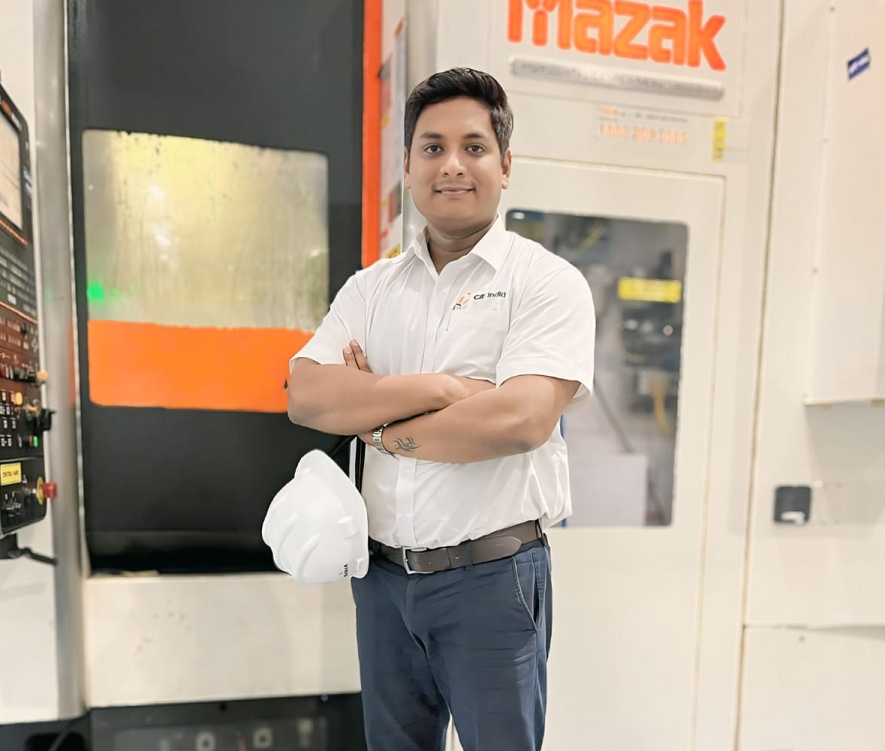